1
Examples Insulation Thickness Based on Economics
Economical insulation thickness based on the” Minimum Total Cost Method” and” Discounted Payback Period” are explained by practical examples. For economic insulation thickness calculations financial input requirements, data input for all calculations and other parameters are explained and given.
2
Insulation Thickness Based on the Minimum Total Cost Method
2.1
Introduction
Insulation of a system implies capital expenditure. In any insulation system it is important to analyse the thermal insulation with respect to cost. There is a definite economic limit to the amount of insulation, which is justified.
The simplest method of analysing the extent of insulation is by comparing the cost of energy losses with the cost of insulating the pipe or equipment. The insulation thickness for which the total cost is the minimum is termed as economic thickness.
For understanding the preferred method of calculating the economic insulation thickness there are two costs associated with the insulation type chosen. For any given thickness, there is:
- The cost of the insulation itself; and
- The cost of the energy lost through the insulation.
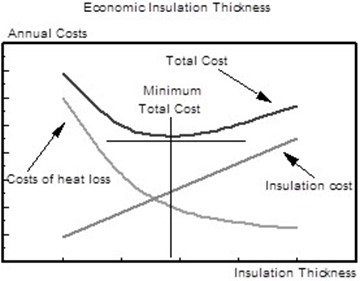
Figure 1: Cost Associated with Insulation Thickness and Heat Loss
In figure 1, the total cost line is drawn for several different thicknesses of insulating material. The economic insulation thickness will be the thickness corresponding to the minimum point on the total cost line.
When two of more layers of insulation are used, each layer may have its own minimum.
The total cost for a given thickness is the sum of both costs, that is, they shall be compared in similar terms.
Therefore, the cost of insulation shall be estimated for each year (= Capital Cost x Capital Service Factor) and shall be compared to the average annual cost of energy losses over the expected life of the insulation.
The graph does not start at zero because the normal minimum possible insulation thickness is 25 to 30 mm (except for sprayed insulation or thinner special insulation materials).
2.2
Equations explained
The bases is already introduced in 2.1
Equation 1:
(Capital Cost × Capital Service Factor) + Annual Operating Cost = Total Cost
Remark: This is the overall equation.
In figure 1, the total cost line is drawn for several different thicknesses of insulating material.
The economic insulation thickness will be the thickness corresponding to the minimum point on the total cost line. When two of more layers of insulation are used, each layer may have its own minimum.
The Minimum Total Cost Method is particularly useful when more than one layer of insulating material is expected, since the results can be presented graphically, and the minimum or minima are immediately obvious. Three values need to be calculated:
- Capital Cost.
- Capital Service Factor; and
- Annual Operating Cost.
Calculation of Capital Cost
The Capital Cost can be calculated according:
Equation 2:
Capital Cost = (Ip × Fr × Fc + s × Fa) × Fi in EUR/j × m1 of m2 (2)
Where:
Ip is the insulation price per unit of flat surface (m2) or unit of pipe length (m1). The value given should include:
- The current price of insulation;
- Fastening and weather-proofing materials;
- Installation;
- Packing;
- Transport and tax costs (variable costs);
- The values should exclude scaffolding and metal surface preparation costs, for example rust removal and painting (fixed costs).
Fr is the currency rate required to express costs in Euro (EUR), or the appropriate local currency (for this guide the ¿ (Euro) is used in the examples);
Fc is the complexity factor. Normally prices are quoted for straight line piping. The complexity factor allows for the extra cost incurred due to fittings. (See Table 1);
s is the insulation thickness in meters;
Fa is an additional cost which is added to the insulation price in certain cases to cover the costs of building pipe-racks, increased civil work, bigger platforms, and so on. An indication of the additional costs are:
- 700 EUR/m of insulation thickness for diameters ≤ 20 inches, for example piping;
- 350 EUR/m of insulation thickness for diameters > 20 inches, for example vessels/columns; and;
- Nothing to be added for very large diameters, for example tanks.
Fi is the investment escalation factor which escalates the present insulation costs to the actual costs at the time of installation.
Piping Complexity Code and Factors
The complexities of table 1 are defined as:
- None: No fittings or prices of fittings are already included.
- Simple: 10 fittings every 30 m (100 feet) of pipe.
- Average: 15 to 20 fittings every 30 m (100 feet) of pipe.
- Complex: 30 to 40 fittings every 30 m (100 feet) of pipe.
2.2
Notes:
Tabel 1: Factoren voor de complexiteit van leidingen
Complexity Code | 0 | 1 | 2 | 3 |
Complexity Factor | None | Simple | Average | Complex |
Pipe size, inches 1 | 1.00 | 1.20 | 1.30 | 1.60 |
2 to 3 | 1.00 | 1.15 | 1.20 | 1.35 |
4 to 6 | 1.00 | 1.10 | 1.15 | 1.25 |
8 to 12 | 1.00 | 1.12 | 1.15 | 1.28 |
12 and above | 1.00 | 1.15 | 1.20 | 1.30 |
- The above factors apply only to welded piping with flanged valves and line pipe flanges. For welded piping with no flanges use an average piping complexity factor of 1.05. These factors are not to be used when valves and flanges are not to be insulated.
- Fittings are denoted as:
- Flange pair: 1 fitting.
- Valve flanges: 2 fittings.
- Valve body: 1 fitting.
- Elbows, tees, reducers, and so on: 1 fitting.
Calculation of Capital Service Factor
The Capital Service Factor is calculated according to the VDI 2055. As there are three different methods explained in the VDI 2055, one of the methods should be known at the beginning of a project.
The methods are explained hereof.
The capital service factor b contains depreciation or repayment (n expected service life in years), interest rate z, maintenance r and general cost g percent are defined as equation (3):
b = (anual fixed cost)/(investment for the insulation) (3)
For the determination of the capital service factor different approaches are used. The values are inserted into these formulas in (per annual year) and they relate to the investment for the insulation.
a) Addition (in 1/a):
b1 = 1/n+1/100×(z+r+g) in 1/a
Where:
n expected service life, in a (”years”)
z interest rate, in %
r maintenance, in %/a
g overhead, in %/a
b) as a, however, instead of the full interest rate only: in %/a is inserted to take the repayment over the service life into account:
b2 = 1/n+1/100×((z+1)/2+r+g) in 1/a
c) Annuity:
b3 = (z/100)/(1-(1/(1+z/100))^n )+(r+g)/100 in 1/a
The interest rate z may be either a company-internal interest rate or an external interest rate. Often r+g (maintenance and overhead) is taken 2%.
In general, the last method should be used or as otherwise determined by the financial department. It is always recommended to involve financial experts on this subject.
For insulation projects, the economic lifetime of the insulation is usually taken to be 10 years, although this lifetime can vary depending on the inspection requirements of local authorities.
Other factors affecting the Capital Service Factor (b) are CAPEX phasing, depreciation, tax rate at margin, inflation and increases in heat cost.
The Capital Service Factor (b) should be defined for each project.
The maintenance percentage (r), which is as default 1% may be changed into higher percentages depending on the complexity of the process facility.
For overhead percentages (g) 1% should be maintained or as recommended by the financial department.
Calculation of Annual Operating Cost
The Annual Operating Cost can be calculated according to equation (4):
Annual Operating Cost = (Ft×Hc×Q×N)×f in €/y×m1 or m2 (4)
Where:
Ft is a conversion factor, which is required to convert the units J/s.m2 or J/s.m1 into GJ/day.m2 or GJ/day.m1 since the heat cost is given in /€GJ. The conversion factor (Ft) has the value: 3600×24/1,000,000,000
Hc is the heat cost which varies according to the heating medium used. Piping and equipment which can be related to a certain heating medium shall be insulated with the economic insulation thickness calculated for that heating medium. The following heating media can be used (prices are indicative and should be checked).
- Refinery fuel;
- LP steam, condensing temperature between 130 °C – 180 °C;
- MP steam, condensing temperature between 180 °C – 250 °C;
- HP steam, condensing temperature above 250 °C;
- Heat Transfer Fluid (HTF) system;
- Emission CO2 op top of above mentioned media (if applicable);
- The heat cost of refinery fuel can be calculated as follows:
- Refinery fuel price, for example, 150 €/ton = 0.150 €/kg;
- Lower heating value 0.0402 GJ/kg, Efficiency 0.88;
- Heat cost = 0.150/ (0.0402 * 0.88) = 4.24 €/GJ;
- The heat cost of LP, MP and HP steam are related to the cost of refinery fuel and should be higher than the heat cost for refinery fuel.
- The emission cost of CO2 should be added to the heat cost price.
A standard point of discussion is the value of heat cost related to surplus steam, associated gas, heavier oil fractions, and so on. Before deciding to take the advantage of the apparently low heat cost value of these alternatives, the following points shall be considered: auditing of utilities, future extensions, town heating, more effective use of gas, environmental conditions, and so on.
When the heat cost is genuinely very low, then only insulation for personnel protection, process or acoustic reasons may be required.
Since the economic insulation thickness is required to be specified at a very early stage of the project (to be able to fix the width of pipe bridges and tracks), the assumed heat cost shall be correct or even on the conservative side. This is because changes later on which result in an increased insulation thickness, are almost impossible to achieve.
Q is the heat loss per unit of flat surface (m2) or unit of pipe length (m1). The calculation of the heat loss will be explained in the next section.
N is the number of working days per year. Scheduled shutdowns should be taken into account. For batch processes it is important to know whether equipment is allowed to cool down between batches or whether the temperature has to be maintained.
F is the price variation factor that will be determined with the following equation:
F = S1/S2 (5)
S1 = (1-((1+p/100)/(1+z/100))^n)/(1-(1+p/100)/(1+z/100)) (6)
Note: For p=z follows a limit S1 = n
S2 = (1-(1/(1+z/100))^n)/(1-1/(1+z/100)) (7)
Note: For p=z follows a limit S1 = n
Where: n expected service life, in a (”years”) z interest rate, in % p price change factor, in percent
2.2
Heat Loss
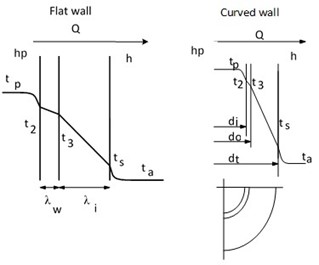
Figure 2: Symbols Heat Loss Calculations Flat & Curved Wall
This section covers the background and calculation of the variable, Q, or heat loss that is required to calculate the annual operating cost. Details and background can be found in a separate document ”Thermal Insulation Calculations”.
If we consider a flat insulated wall with a hot process medium on one side and ambient air on the other, heat flows from the hot medium, through the wall and insulation, to the air. The heat loss, Q, depends on the following heat flow resistances that have to be overcome:
- (1/hp) is the fluid heat transfer resistance from the hot medium to the wall. This resistance is only important if the medium is a gas, a stagnant medium, a medium with a low velocity or in the case of a bare wall heat loss calculation. In other cases, where the resistance is small in relation to the insulation resistance, the fluid heat transfer resistance may be ignored.
- (δw/λw) is the wall resistance that is very small compared to the other resistances and can usually be neglected. Exceptions are stainless steel wall materials, other wall materials with low thermal conductivity, and when bare wall heat loss calculations are performed.
- (δi/λi) is the insulation resistance that is the most important figure when calculating the heat loss through an insulated wall. An error in the thermal conductivity of the insulating material will result in a noticeable difference in the optimum economic insulation thickness. The thermal conductivities, as supplied by the manufacturers, have to be corrected for the type of application of the insulation. (See Table 2).
- (1/h) is the air heat transfer resistance from the surface to the air. Although the importance of this resistance decreases with an increasing insulation thickness, it should not be ignored.
2.2
Table 2: Recommended Allowance for Thermal Conductivity Insulation Materials
Type of Material/Application | Allowance (in %) | |
1 | For all insulation, for insufficient application and tolerances on standard test conditions according to certificate. | 5 |
2a | For loose filling with metal supports on flat walls, piping and equipment, supports at 350 mm. | 25 |
2b | For loose filling with ceramic supports on flat walls, piping and equipment, supports at 350 mm. | 15 |
2c | For blankets with ceramic supports at distances of 500 mm. | 10 |
2d | For blankets with ceramic supports at distances of 500 mm, but last insulation layer over the supports, blankets of this layer being sufficiently connected to each other. | 6 |
2e | For blankets without supports, blankets of each layer being sufficiently connected to each other. | 2 |
2f | For preformed pipe and board insulation with staggered joints. | 2 |
2g | For insulation of equipment with uninsulated protruding metal parts, e.g. cleats, piping, instrumentation etc., depending on situation. | 20 tot 30 |
3a | For insulation materials without a certificate. | 20 |
3b | For a very good construction with pipe hangers. | 1 |
3c | For a good pipe support construction. | 2 |
The heat flux through an insulated flat wall is directly proportional to the temperature difference between hot and cold side and indirectly proportional to the thermal resistance.
Since the heat flux through each section must be equal, the following
Equation | Unit | Number Equation |
Q = ((tp-t2))/(1/hp) | W/m2 | (8a) |
Q = ((t2-t3))/(δw/λw) | W/m2 | (8b) |
Q = ((t3-ts))/(δi/λi) | W/m2 | (8c) |
Q = ((ts-ta))/(1/h) | W/m2 | (8d) |
By adding the temperature differences in equations (8a) to (8d), an overall equation can be found, in terms of just the product-bulk and ambient-air temperatures. The equation is as follows:
Equation: Q = ((tp-ta))/(1/hp+δw/λw+δi/λi+1/h) in W/m2 (9)
For a curved wall a similar set can be derived.
(10)
(11)
(12)
(13)
2.2
This can be rewritten as Equation (14):
(14)
* ln = natural logarithm
In the case of a multi-layer application with different insulation materials, equation (4c) and (6c) shall be repeated for each layer. The same can be done if the temperatures between different layers of the same material have to be calculated.
If necessary, a fouling coefficient can be added, by repeating equation (4a) and (6a) for the fouling layer.
This fouling coefficient will only be important for un-insulated piping and equipment, or for calculating the heat loss of a tank bottom.
The thickness of the fouling layer at the bottom of a tank can be 1 or 2 m just before cleaning. The reversed value of the fouling coefficient is called the fouling resistance.
The above equation specifies the heat loss for a curved wall per meter length (m1).
When the heat loss of a pipe is expressed in square meters (m2), it should be indicated to which diameter this heat loss is related.
To calculate the heat loss of a curved wall in , the heat loss calculated in accordance with equation (7) should be divided by λ∗De when the heat loss is related on the outer surface of the insulation, and by λ∗Di when the heat loss is related to the inside diameter of the pipe.
The film coefficient of the medium can be calculated according to ISO 12241, VDI 2055 or other sources. In table 3 indications are given for the film coefficient, depending on the medium.
Table 3: Indicative film coefficients of different mediums
Condensing steam | > 4.000 | W/m2 × K |
Condensing HC vapours | 2000 to 4000 | W/m2 × K |
Liquids, low viscosity | 500 to 4000 | W/m2 × K |
Gases and other liquids | 50 to 500 | W/m2 × K |
Stagnant fluids | 10 to 200 | W/m2 × K |

hr is the contribution of radiation to the total air side film coefficient. It depends on emissivity from the outside surface. The emissivity from a surface is the measure of its ability to emit radiant energy relative to a black body (table 4).
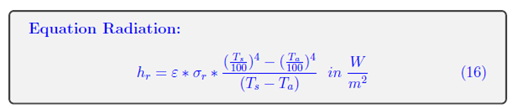
Note: More emissivity factors can be found in de VDI 2055 or CINI manual.
Where:
ε is the emissivity of the outside surface [-].
σr is the Stefan-Boltzmann constant and is: 5.67*10-8
Ts is the outer surface temperature [°K].
2.2
Table 4: Emissivity factors
Surface | Emissivity ε |
Aluminium, bright rolled | 0.05 |
Aluminium, oxidized | 0.13 |
Galvanized sheet metal, blank | 0.26 |
Galvanized sheet metal, dusty | 0.44 |
Austenitic steel | 0.15 |
Aluminium-zinc sheet | 0.18 |
Non-metallic surfaces | 0.94 |
The heat transfer coefficient hr may be ignored for:
- heat transfer from flowing medium;
- inside pipes/equipment (radiation equilibrium); and
- for small temperature differences.
Especially the last condition is important, as the outer insulated surface temperature is close to the ambient temperature. Care needs to be taken that the outer surface temperature will be < 60 degrees Celsius. Otherwise personnel protection is required. Therefore, the outer surface temperature shall always be checked.
hcv is the contribution of convection to the total air side film coefficient.
The equations most frequently used are those according ISO 12242 (or the VDI 2055 or ASTM C680).
The requirements and results of equations 8 and 9 to determine the external film coefficient h=hr+hcv in W/m2*K should be obtained from ISO 12241-4.1.3.
2.3
Economic Insulation Calculation: Example
This section contains an example of the minimum total cost method of calculating the economic insulation thickness.
A limited set of input data is specified, which is the minimum required. In the case of indirect input data the resulting value is given, for example, Capital Service Factor. For other data, more information can be found in tables 1, 2, 3 and 4.
The example is not fully worked out in detail, but is shown to give an indication of the results that can be obtained. Al input should be checked by the financial, process and engineers.
For the example, the following input data is used:
Table 5: Data Economic Insulation Calculation Example
Complexity: | Average | Additional Cost: | 200 €/m1 |
Investment escalation factor: | 1.2 | Capital Service Factor: | 14,5% (b2: depreciation) |
Maintenance Factor: | 1%/a | Service Life: | 10 years |
Overhead Factor: | 1.2 | Interest Rate: | 4%/a |
Complexity factor: | 1.2 | Yearly average ambient temperature: | 10 °C |
Product Temp: | 200 ◦C | Yearly average wind velocity: | 5 m/s |
Film coeff. inside: | 4000
W/m2*K |
Operating days/year: | 330 days |
Heat cost (including CO2): | 10.00
EUR/GJ |
Price change factor heat cost: | 2%/a |
Pipe diameter: | 219 mm (8 Inches) | Wall Thickness: | 8,2 mm |
Thermal cond. wall | 50
W/m*K |
Surface Aluminised Steel: | ε = 0.4 dof |
Surf. bare pipe: | ε = 0.8 | Insulation: | Rock wool pipe sections |
Thermal conductivity | 0.0468 W/m*K | according CINI Tab6: | polynomial used with safety factor |
The economic insulation thickness can be calculated with the mentioned equations hereof. In the first instance, however, it should be checked whether insulation is actually required.
Therefore, the first step is to calculate the heat loss, and hence the cost of heat loss, of the bare pipe using the applicable equations.
Remark: Normally for simplification of the calculation, the resistances over the boundary layer on product side and the pipe wall may be ignored.
The temperature at the outer wall surface is assumed to be equal to the product temperature and may be used to calculate the heat transfer coefficient due to radiation. The emissivity for cladding can be found in table 4 (more can be found in the CINI Manual or VDI 2055). For the bar surface of the pipe ε = 0.8 is adopted.
Air side coefficient (convection + radiation) bar surface:
h = hr + hr = 10.30 + 44.10 = 54.40 W/m2 ×K
Heat loss bare surface: 7111 W/m1
Cost of energy (for 330 days/year):
Annual operation cost (heat loss): 2027.49e/m1 ×y
The capital cost and the annual operating cost (energy cost) together with data required to follow the calculation sequence are given in table 5. Again, not all intermediate results are shown.
The piping complexity factor can be found in table 1 and the allowance for type of material and application with respect to the thermal conductivity in table 2.
The resistance over the boundary layer on air side is once again ignored. This means that in part of internal film coefficient and pipe wall are neglected in equation 14 , only the resistance over the insulation layer for a curved wall and external film coefficient is used.
2.3
Table 6: Data Minimum Cost Method
Insulation Thickness | (mm) | 60 | 70 | 80 | 100 | 110 | 120 |
Insulation Price | (EU R/m1) | 59.60 | 67.20 | 74.80 | 90.00 | 97.60 | 105.20 |
Investment cost Insulation | (EU R/m1) | 114.62 | 130.37 | 146.11 | 177.60 | 193.34 | 209.09 |
Capital (Inv. Cost*CSF) | (Inv.Kosten*CSF) | 16.62 | 18.90 | 21.19 | 25.75 | 28.03 | 30.32 |
Heat Loss | (W/m1) | 125.99 | 111.63 | 100.76 | 85.38 | 79.72 | 74.97 |
Cost of energy | (EU R/m1*y) | 31.27 | 27.70 | 25.01 | 21.19 | 19.78 | 18.60 |
Min. Total cost | (EU R/m1*y) | 47.89 | 46.61 | 46.19 | 46.94 | 47.82 | 48.92 |
Above is plotted into a curve (see figure 3 )
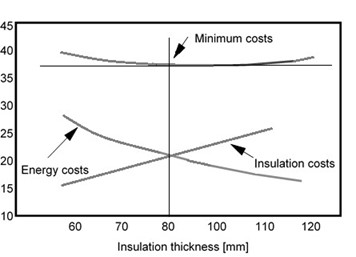
Figure 3: Graph of Insulation Thickness against Annual Costs
Although the curves for the capital cost and the energy cost are rather steep, the curve of the total cost is almost flat near the optimum.
This explains why the insulation thickness may be rounded off to the nearest manufacturer’s standard thickness. In this case 80 mm insulation thickness could be used.
If the resistances over the boundary layers of the product and air, and the resistance through the pipe wall are included in the calculations, it can be seen that, although there are small changes in the heat loss value, the optimum insulation thickness hardly changes.
However, since the curve is so flat around the optimum insulation thickness, the question remains whether it really makes much difference if a smaller, and hence cheaper, thickness is installed.
The answer to this question should be NOT to deviate from the economic insulation thickness since the cost of retrofitting, if an insufficient insulation layer has been installed in the first instance, will be a multiple of the cost of installing the correct thickness straight away.
Examples of these extra costs are: making space on bridges, increasing supports, increasing bushings, expanding straight length of protruding nozzles, waste of the existing insulation material and sheeting, and so on. Retrofitting can only be justified for technical reasons and not on economic grounds.
3
Discounted Payback Period
The discounted payback method takes into account the time value of money and is therefore an upgraded version of the simple payback period method. Companies use this method to assess the potential benefit of undertaking a particular business project. In this case the project cost of insulation and related fixed heat cost should be taken into account, against the heat loss cost of the bar surface (”non-insulated piping/equipment”).
3.1
Example Discounted Payback Period
For input the same information of the minimum total cost method is used and as example the economical thickness of 80 mm is taken, along with all related calculations.
Table 7: Data Discounted Payback Period
Heat Loss Cost Bar Surface Pipe: 1765 e/m1.y |
Heat Loss Cost Insulated Pipe: 25 e/m1/y |
Insulation Thickness: 80 mm |
Investment cost insulation: 146 e/m1
This is including additional cost, investment escalation factor, maintenance factor, overhead factor, complexity factor (the same data as 5). |
Service life: 10 years |
Discount Rate: 11 % |
Operating days: 330 days |
&nsbp;
What is the Discounted Payback Period (DPP)?
The discounted payback period is a measure of how long it takes until the cumulated discounted net cash flows offset the initial investment in an asset or a project. In other words, DPP is used to calculate the period in which the initial investment is paid back.
In project management, this measure is often used as a part of a cost-benefit analysis, supplementing other profitability-focused indicators such as internal rate of return or return on investment. It can however also be leveraged to measure the success of an investment or project in hindsight and determine the point at which an initial investment has actually paid back.
The discounted payback period is calculated by discounting the net cash flows of each and every period and cumulating the discounted cash flows until the amount of the initial investment is met. You will find the formula in reference: 17. This requires the use of a discount rate which can be either a market interest rate or an expected return. Some organizations may also choose to apply an accounting interest rate or their weighted average cost of capital. While the discounted payback period is still a comparatively handy indicator, it is more precise than the generic payback period as it considers the time of the occurrence of cash flows. Discounting the cash inflows of the project for each period at a suitable discount rate.
How is the Discounted Payback Period Calculated (DPP)?
The formula to calculate the discounted payback period is:
DPP = y + ABS(n)/p (17)
Where: y = the period preceding the period in which the cumulative cash flow turns
positive,
p = discounted value of the cash flow of the period in which the cumulative cash flow is => 0 abs(n) = absolute value of the cumulative discounted cash flow in period y.
The equation is worked out in a spreadsheet, the outcome is shown in table 8
3.1
Table 8: Discounted Payback Period (DPP) for piping
Investment | €1843 | Discount Rate
11% |
||
Year | Cash Flow in € | Present Value Factor | Discounted CF | Cumulative Discounted |
0 | -146 | 1000 | -146 | -146 |
1 | 1740 | 0.9009 | 1568 | 1422 |
2 | 1740 | 0.8116 | 1412 | 2834 |
3 | 1740 | 0.7312 | 1272 | 4106 |
4 | 1740 | 0.6587 | 1146 | 5252 |
5 | 1740 | 0.5935 | 1033 | 6285 |
6 | 1740 | 0.5346 | 930 | 7215 |
7 | 1740 | 0.4817 | 838 | 8053 |
8 | 1740 | 0.4339 | 755 | 8808 |
9 | 1740 | 0.3909 | 680 | 9488 |
10 | 1740 | 0.3522 | 613 | 10101 |
DPP = 0+146/1568 = 0.10 year ∼ 38 days
The payback period of 38 days is not a realistic scenario and therefore is this method not suitable for the calculation of economical insulation calculated with this kind of input. More interesting is if in cases like additional heat losses the capacity of e.g. gas turbines or boil off compressors need to be increased or by thicker insulation it could be decreased. The Discounted Payback Period is often mentioned and used as a measure for the viability of projects. In this case the capacity of turbines or compressors.
Therefore the use of the Discounted Payback Period should be discouraged when calculating an economic insulation thickness. This is because it does not involve all factors (as mentioned above), used in the ”Minimum Total Cost” method. Therefore, it does not take into account the changing value of money over time. In short, the Discounted Payback Period should only be used for very broad-brush screening and not for the final choice of insulation thickness. Therefore a more better example is taken. In this example the Discounted Payback Period is a valid instrument.
3.1
DPP Tank farm Roof Insulation
Given: A tank farm with 8 oil tanks (fixed roof tanks) of which is investigated if insulation of the tank roofs is a savings-potential.
Table 9: Information Tanks for determining DPP
Tank roof insulation: | Rock Wool thick: 100 mm |
Heat Loss non-insulated roof: | 80 W/m2 |
Heat Loss Insulated roof: | 10 W/m2 |
Energy saving: | 12.500 MWJ/Year |
Reduction (saving) cost: | €650.000 |
Price insulation: | €90/m2 |
Total m2 roof insulation: | 17.500 m2 |
Investment: | €1.575.000 |
Discount rate: | 10 % |
3.1
Question: Determine discounted payback period (DPP), based on a service life of 10 years.
Solution:
Table 10: Discounted Payback Period (DPP) Tank
Investment | €1.575.000 | Discount Rate
10% |
||
Year | Cash Flow
in € |
Present Value Factor | Discounted CF | Cumulative Discounted |
0 | -1.575.000 | 1000 | -1.575.000 | -1.575.000 |
1 | 650.000 | 0.9091 | 590.909 | -984.091 |
2 | 650.000 | 0.8264 | 537.190 | -446.901 |
3 | 650.000 | 0.7513 | 488.355 | 41.454 |
4 | 650.000 | 0.6830 | 443.959 | 485.413 |
5 | 650.000 | 0.6209 | 403.599 | 889.011 |
6 | 650.000 | 0.5645 | 366.909 | 1.255.919 |
7 | 650.000 | 0.5132 | 333.553 | 1.586.472 |
8 | 650.000 | 0.4665 | 303.230 | 1.892.702 |
9 | 650.000 | 0.4241 | 275.663 | 2.168.365 |
10 | 650.000 | 0.3855 | 250.603 | 2.418.969 |
DPP = y + abs(n)/p = 2 + 446.901/488.355 = 02.93 years
A discounted payback period of less than 3 years is very attractive for this project and justified to continue with this project.