1
INTRODUCTION
In the market several computer programs are available to perform heat transfer calculations to determine the insulation thickness. The insulation manufacturer, the contractor and client, they all have their own software. However, these programs are not always applicable for all types of insulation material and sometimes could give different results.
Therefore, the software should clearly indicate which standard is used for the calculation or which deviations are used to arrive to the results. For all calculation methods the following standards may be used:
- ISO 12241 (third edition 2022-06) Thermal insulation for building equipment and industrial installations — Calculation rules;
- ASTM C680 -19 Standard Practice for Estimate of the Heat Gain or Loss and the Surface Temperatures of Insulated Flat, Cylindrical, and Spherical Systems by Use of Computer Programs.
- VDI 2055 Part 1: “Thermal insulation of heated and refrigerated operational installations – Calculation rules”
CINI releases the CINICALC software. CINICALC allows the user to perform many of the thermal insulation calculations as prescribed in this chapter. In addition to these calculations, specific calculations can also be performed as described in section 2.4. Furthermore, CINICALC can calculate the heat losses at different insulation thicknesses and the CO2 reduction can be taken into account by insulating pipes and equipment.
2
CALCULATIONS
2.1
Calculation program insulation thickness and process temperatures
With a calculation program the required insulation thickness for the full range of operating temperatures can be calculated, for all line pipe diameters and flat walls. The results are mostly presented in a table. The calculated results contain not only the required insulation thickness, but also intermediate results, such as the heat loss, the thermal conductivity, emission etc. can often be shown. General insulation thickness calculations can be split up in two groups, i.e. heat insulation and cold insulation; both groups can be approached from different points of view.
2.2
Heat Insulation (with the objective to reduce heat loss)
A – Economic insulation thickness
The optimum economic insulation thickness is calculated according to the “Minimum Total Cost Method”. For a given thickness the total cost is the sum of the cost of the investment itself and the cost of the energy lost through the insulation. (see section 4.1). Alternatively , especially for e.g. tanks, the “Discounted Payback Period ” could be applied (see section 4.2).
B – Personnel Protection
The calculation of the insulation thickness required for personnel protection is based on limiting the surface temperature to the maximum allowable value. This is a safety requirement. Basis is the maximum surface temperature of 60°C (Ref. CINI 1.3.19);at higher temperatures personnel protection is required. For assessment for this safety requirement the following standards should be consulted:
- ASTM C1055 Standard Guide for Heated System Surface Conditions that Produce Contact Burn Injuries;
- ASTM C1057 Standard Practice for Determination of Skin Contact Temperature from Heated Surfaces Using a Mathematical Model and Thermesthesiometer.
2.3
Cold Insulation (with the objective to reduce heat gain)
A – Preventing surface condensation
When the process temperature is below the maximum ambient temperature, the minimum required insulation thickness which prevents surface condensation is calculated.
B – Maximum Heat Gain
When the process temperature is below the maximum ambient temperature, the minimum insulation thickness is calculated required to achieve the maximum allowable heat gain.
2.4
Case-by-Case calculations
For projects the above mentioned general calculation methods can be performed and the results may be implemented for the full scope of the project. In specific cases insulation may be required for process reasons e.g. in case where heat losses beyond a certain margin affect the process or product. For instance a long line with superheated steam whose temperature must not drop below a certain limit, or a heat loss which should always remain restricted even when the product flow stagnates or during the coldest period in a year. A separate insulation thickness evaluation is needed to fulfil such specific process, safety, environmental or technical requirements. In such specific cases the following calculations may be required:
- The temperature change of a flowing fluid in an insulated or un-insulated pipe line or equipment.
- The time in which a stagnant fluid in an insulated or an un-insulated pipe line or equipment changes to a certain temperature.
- The temperature change of a stagnant fluid in an insulated or an un-insulated pipe line or equipment in a certain time.
- The insulation thickness for a pipe line or equipment to limit the temperature change of a flowing fluid to a certain value.
- Heat losses in pipelines or equipment.
- Freeze protection of insulated pipelines and equipment
Note: Product may be gas, damp, 2 phase or liquid.
3
HEAT TRANSFER
For the principles of heat transfer calculations reference is made to ISO 12241, ASTM C680 or VDI 2055 Part 1. In cases those standards does not cover the specific situation the theory of heat transfer as stated in the textbooks may be used, as long as the source is clearly indicated.
4
HEAT INSULATION
The insulation thickness can be calculated from two different premises, i.e. the economic insulation thickness and personnel protection. The principle calculations are given in ISO 12241, ASTM C680 or VDI 2055 part 1,
4.1
Economic Insulation Thickness
The insulation thickness is determined by the relation between several costs. There are three costs (life cycle costs) associated with the insulation system selected. For any given thickness, there is:
- The cost of the insulation proper i.e. Capital Cost
- The cost of the energy lost through the insulation.
- The cost of maintenance.
The life cycle cost for a given thickness is the sum of above costs: this means that they shall be compared in similar terms. Therefore the cost of insulation shall be estimated for each year: (Capital Cost x Corrected Capital Charge) and must be compared to the average annual cost of energy losses over the expected life of the insulation. The optimum economic insulation thickness can be calculated using the following method:
x
The Minimum Total Cost Method: Total Cost = (Capital Cost x Corrected Capital Charge) + Annual Operating Cost (equation 1)
x
The economic insulation thickness will be the thickness corresponding to the minimum point on the total cost curve.
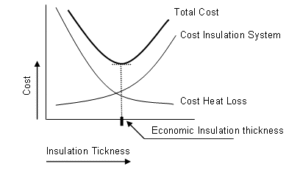
The Minimum Total Cost Method is the preferred calculation method. It is particularly useful when more than one layer of insulating material is expected, since the results can be presented graphically and the minimum or minima immediately can be observed. Three values need to be calculated:
- Capital Cost
- Corrected Capital Charge
- Annual Operating Cost
Capital Cost = (Ic × Fr × Fc + di × Fa) × Fi EUR/y.m1 of m2 (equation 2), where:
- Ic is the insulation costs per unit of flat surface or unit of pipe length. The value should include the current price of insulation and finishing materials, installation, packing, transport and tax costs (variable costs), but exclude scaffolding and metal surface preparation costs e.g. rust removal and painting (fixed costs).
- Fr is the currency rate required to express costs in Euro (EUR), or another appropriate local currency.
- Fc is the complexity factor. Normally prices are quoted for straight-line piping. The complexity factor allows for the extra cost incurred due to fittings.
Complexity factor | |||||
---|---|---|---|---|---|
Complexity | None | Simple | Average | Complex | |
Pipe diameter in OD in mm inches |
|||||
21.3 to 48.3 | ½ tot 1½ | 1.00 | 1.20 | 1.30 | 1.60 |
60.3 to 88.9 | 2 tot 3 | 1.00 | 1.15 | 1.20 | 1.35 |
114 to 168 | 4 tot 6 | 1.00 | 1.10 | 1.15 | 1.25 |
219 to 323 | 8 tot 12 | 1.00 | 1.12 | 1.15 | 1.28 |
≥ 355 | ≥ 14 | 1.00 | 1.15 | 1.20 | 1.30 |
The complexity is defined as:
- None: no fittings included
- Simple: less than 10 fittings every 30 m (100 feet) of pipe
- Average: 10 to 20 fittings every 30 m (100 feet) of pipe
- Complex: 20 to 40 fittings every 30 m (100 feet) of pipe
A flange pair, a valve body, elbows, tees and reducers etc. are counting for 1 fitting each, e.g. a flanged valve will count for 3 fittings i.e. 2 flange pairs + 1 body.
di is the insulation thickness in meters
Fa is an additional cost which is added to the insulation price in certain cases to cover the costs of building wider pipe-racks, increased civil work, bigger platforms etc. Nothing to be added for very large diameters e.g. tanks.
Fi is the investment escalation factor which up-dates existing insulation costs to present insulation costs. The investment escalation factor is normally set at 1.0.
A Capital Charge may be applicable to the Capital Cost in case local authorities or governments for energy conservation projects offer fiscal and investment incentives. Since the maintenance cost is taken to be a certain percentage of the capital expenditure as well, this maintenance percentage may be added to the Capital Charge to give the Corrected Capital Charge.
The Annual Operating Cost can be calculated according to the following equation: Annual operating cost = Ft × Hc × Φ × N EUR/y.m1 of m2 (equation 3), where:
Ft is a conversion factor which is required to convert the units J/s.m2 or J/s.m1 into GJ/day.m2 or GJ/day.m1, since the heat cost is given in EURO/GJ. The conversion factor (Ft ) has the value: 3600 x 24 / 1.000.000.000. The CO2 emission should be taken into account as well. The CO2 emission conversion should be taken into account as well. The CO2 tax links a price to the industrial emission of one ton of CO2. The rate therefore applies per ton of CO2 emitted and should be converted to a kWh price as stated in section 6.
Hc is the energy cost, which varies according to the heating medium used. A standard point of discussion is the value of heat cost related to surplus steam, associated gas, heavier oil fractions etc. Before deciding to take the advantage of the apparently low heat cost value of these alternatives, the following points must be considered: CO2 emissions, public utilities, future extensions, town heating, more effective use of gas, environmental conditions etc. When the heat cost is genuinely very low, then only insulation for personnel protection, process or acoustic reasons may be required.
Q is the heat loss per unit of flat surface (m2) or unit of pipe length (m1).
N is the number of working days per year. Scheduled shutdowns should be taken into account. For batch processes it is important to know whether equipment is allowed to cool down between batches or whether the temperature has to be maintained.
In CINI 6.1.02 (informative) an example of the minimum cost method is given.
4.2
Economic Insulation Thickness based on the “Discounted Pay Back Period”
The discounted payback method takes into account the time value of money and is therefore an upgraded version of the simple payback period method. In this case the project cost of insulation and related fixed heat cost should be taken into account, against the heat loss cost of the bar surface (”non-insulated piping/equipment”).
For input the same information of the minimum total cost method is required, such as:
- Heat Loss Cost Bar Surface Pipe in EUR/m1.y
- Heat Loss Cost Insulated Pipe in EUR/m1/y
- Insulation Thickness in mm • Investment cost insulation in EUR/m1
- This is including additional cost, investment escalation factor, maintenance factor, overhead factor, complexity factor.
- Service life in years
- Discount Rate in %
- Operating days in days
Explanation of the Discounted Payback Period (DPP): The discounted payback period is a measure of how long it takes until the cumulated discounted net cash flows offset the initial investment in an asset or a project. In other words DPP is used to calculate the period in which the initial investment is paid back. In project management, this measure is often used as a part of a cost-benefit analysis, supplementing other profitability-focused indicators such as internal rate of return or return on investment. It can however also be leveraged to measure the success of an investment or project in hindsight and determine the point at which an initial investment has actually paid back. The discounted payback period is calculated by discounting the net cash flows of each and every period and cumulating the discounted cash flows until the amount of the initial investment is met.
The formula to calculate the discounted payback period is: DP P = y + abs(n)/p, where:
- y = the period preceding the period in which the cumulative cash flow turns positive;
- p = discounted value of the cash flow of the period in which the cumulative;
- cash flow is => 0 ;
- abs(n) = absolute value of the cumulative discounted cash flow in period y.
This requires the use of a discount rate which can be either a market interest rate or an expected return. Some organizations may also choose to apply an accounting interest rate or their weighted average cost of capital. While the discounted payback period is still a comparatively handy indicator, it is more precise than the generic payback period as it considers the time of the occurrence of cash flows discounting the cash inflows of the project for each period at a suitable discount rate. The method is not suitable for e.g. a single meter pipe, as unrealistic pay back periods are calculated, but for tank parks it is an useful method. In CINI 6,1,02 (informative) an example of the discounted payback period is given.
4.3
Insulation thickness required for personnel protection
In cases where the non-insulated wall temperature is higher than 60 °C and the piping or equipment is within reach of plant personnel, for safety reasons thermal insulation should be used for personnel protection. If insulation is the chosen option for personnel protection, the following design criteria can be used to calculate the required insulation thickness:
- Allowable surface temperature 57°C, based on a 5 sec. exposure time and first degree burn, as indicated in ASTM C1055;
- Maximum ambient temperature;
- Low wind velocity, 0-2 m/s.
When the insulation thickness calculated for personnel protection is more than the economic insulation thickness, then the personnel protection insulation thickness for the whole plant shall be considered. In view of possible corrosion under insulation, preference is given to physical barriers in the lower temperature range (60-250°C), by means of perforated sheeting without insulation material. (see CINI 1.3.19). In specific cases the distances between the hot surface and the perforated sheet shall be calculated with the formulas as mentioned before.
5
COLD INSULATION
For the principles of heat transfer calculations reference is made to ISO 12241, ASTM C680 or VDI 2055-part1.
6
SAVING OF ENERGY AND EMISSION REDUCTION
Savings in energy levels by means of insulation are directly related to savings in emission of CO2, N2O and CH4. The emission levels are related to the source of energy. When the savings of energy are known, the CO2 emission reduction can be calculated..
CO2 emission [kg CO2 ] = CO2-emission factor [kg CO2 /m3 x fuel quantity (m3) (4) The CO2-emission factor (E) depends on the type of fuel (gas, oil, coal, etc.) In calculations of equivalent CO2 emission, next to CO2 emission also the N2O and CH4 emission levels are included with their respectively GWP’s (global warming potential)
CO2 eq. emission = E CO2 x GWP (CO2) + E N2O x GWP (N2O) + E CH4 x GWP (CH4) (5)
Emission | GWP |
---|---|
CO2 | 1 |
N2O | 310 |
CH4 | 21 |
In case of electricity is the energy source, the emission is:
CO2 eq. emission [kg CO2 ] = CO2-emission factor [kg CO2 /kWh] x electricity consumption (kWh) (6)
The CO2–emission factor depends on the blend of electricity, reflecting the several fuel sources (gas, oil, coal, nuclear power etc.) in the power plants and with that the emission of the electric energy production.
7
NOMENCLATUUR ECONOMISCH ISOLATIEDIKTE CALCULATIONS
Name | Symbol | SI-unit |
---|---|---|
Additional cost | Fa | EUR/m1 |
Annual operating cost | — | EUR/j.m1 or EUR/j.m2 |
Capital | — | EUR/j.m1 or EUR/j.m2 |
Complexity factor | Fc | — |
Conversion factor | Ft | — |
Currency rate | Fr | 1 ×× = ××.×× EUR |
Heat cost | Hc | EUR/GJ |
Insulation cost | Ic | EUR/m1 of EUR/m2 |
Investment escalation cost | Fi | — |
Thickness, insulation layer | di | m |
Operating days per year | N | d/j |
8
INPUT DATA
8.1
General applications
Table with input data for general insulation thickness calculations:
4. Maximum heat gain
Description | Calculation case | ||||
---|---|---|---|---|---|
1 | 2 | 3 | 4 | ||
Process data | |||||
Maximum product temperature [°C] |
|
|
|
|
|
Max. allowable surface temperature [°C] |
|
||||
Max. allowable heat gain [W/m2] |
|
||||
External data | |||||
Average yearly ambient temperature [°C] |
|
||||
Design ambient temperature [°C] |
|
|
|
||
Average yearly wind velocity [m/s] |
|
||||
Design wind velocity [m/s] |
|
|
|||
Relative humidity [%] |
|
||||
Air side film coefficient [W/(m2.K)] |
|
|
|
|
|
Calculation method applied |
|
|
|
|
|
Structural data | |||||
Line pipe diameter [m] |
|
|
|
|
|
Selection insulation material [-] |
|
|
|
|
|
Thermal conductivity [W/(m.K)] |
|
|
|
|
|
Allowances on Material / Application |
|
|
|
|
|
Selection jacket material |
|
|
|
|
|
Complexity code |
|
||||
Cost data | |||||
Local Currency [LC |
|
||||
Basic Currency [BC] |
|
||||
Currency Rate |
|
||||
Additional cost [BC/m] |
|
||||
Investment escalation factor |
|
||||
Capital Charge |
|
||||
Cost of heat [BC/GJ] |
|
||||
Operating days a year [days/year] |
|
8.2
Case by case applications
Table with input data for a specific calculation:
- The temperature change of a flowing product in an un-insulated / insulated pipe line
- The time in which a stagnant product in an un-insulated / insulated pipe line changes to a certain temperature
- The temperature change of a stagnant product in an un-insulated / insulated pipe-line in a certain time
- The insulation thickness for a pipe-line to limit the temperature change of a flowing product to a certain value.
Description | Calculation case | |||
---|---|---|---|---|
1 | 2 | 3 | 4 | |
Process data | ||||
Inlet temperature of the product [°C] |
|
|
|
|
Outlet temperature of the product [°C] |
|
|
||
Product flow rate [kg/s] |
|
|
||
Product density [kg/m3] |
|
|
||
Product specific heat [J/(kg.K)] |
|
|
|
|
Inside film coefficient [W/(m2.K)] |
|
|
|
|
Time required for temperature change [s] |
|
|||
External data | ||||
Ambient temperature [°C] |
|
|
|
|
Wind velocity [m/s] |
|
|
|
|
Air side film coefficient [W/(m2.K)] |
|
|
|
|
Calculation method applied |
|
|
|
|
Structural data | ||||
Line pipe diameter [m] |
|
|
|
|
Thickness of pipe wall [m] |
|
|
|
|
Thermal conductivity pipe wall [W/(m.K)] |
|
|
|
|
Length of pipe line [m] |
|
|
||
Selection insulation material [-] |
|
|||
Thermal conductivity [W/(m.K)] |
|
|||
Allowances on Material/Application [-] |
|
|||
Insulation thickness [m] | ||||
Selection jacketing / finishing material |
|
|||
Number of intermediate steps |
|
|
|
8.3
Thermal Conductivity
8.3.1
The thermal conductivity λ, which is applied in the calculation depends on the insulation material and the average temperature in the insulation layer. Since the value is not rectilinear with the temperature (ref. ISO 12241, Figure 1), for the correct calculation of the λ-value shall be established in accordance with the polynomials, based on curve fitting of thermal conductivity tables of the insulation materials as mentioned in TAB 2 of the CINI Manual or as indicated by the tables of the supplier/manufacturer. The best coefficient of determination (R²) should be used. The polynomial could be degree 1,2,3,4 or 5.
In all cases the used material thermal conductivities shall be confirmed by independent certified laboratories. The outcome is always a laboratory measurement. For operational thermal conductivity an allowance is required to deviations in the material and application. The allowances for different insulation materials for pipes and equipment are given in the table below:
Type insulation material | Allowance in %
More than one layer |
Allowance in %
One layer |
Glass Wool slabs/blankets | 10 | 15 |
Glass wool pipe sections | 5 | 10 |
Rock wool slabs/blankets | 10 | 15 |
Rock wool pipe sections | 5 | 10 |
Flexible elastomeric foam |
5 | 10 |
Calcium silicate | 5 | 10 |
Flexible aerogel blanket | 10 | 15 |
Polyisocyanurate | 15 | 20 |
Extruded polystyrene foam |
15 | 20 |
Cellular glass | 5 | 10 |
Expanded perlite | 10 | 10 |
Note: Instead of this table the allowance factors for the determination of the operational thermal conductivity for several insulation materials as stated in the VDI 2055-Part 1-Annex 3, may be used. |